1. Design and Structure:
- Counterflow Configuration: The core design feature of a counterflow heat exchanger is the arrangement of air streams in opposite directions. Typically, this is achieved by using a series of parallel plates or tubes where one stream flows in one direction, and the other flows in the opposite direction.
- Materials: The plates or tubes are usually made of materials with high thermal conductivity, such as aluminum or copper, to maximize heat transfer. Some designs also use plastic for specific applications where corrosion resistance or weight reduction is important.
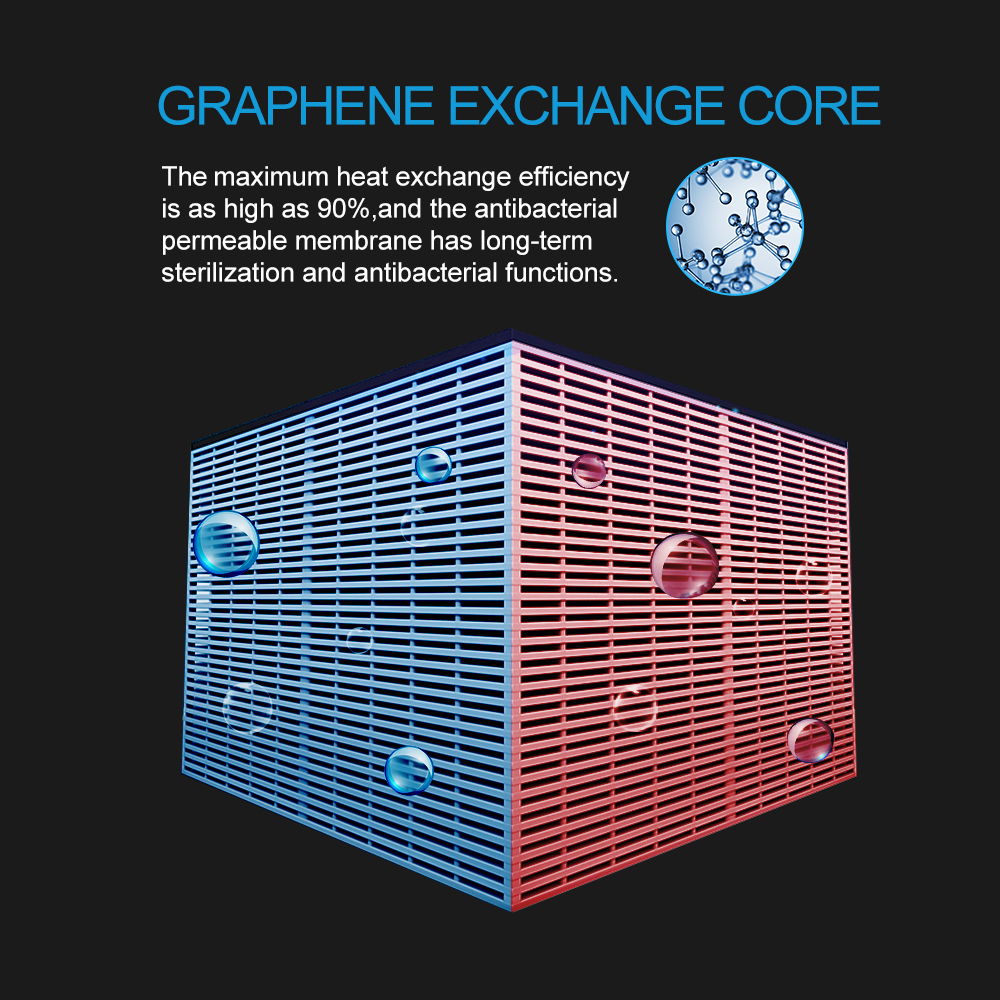
2. Working Principle:
- Heat Exchange Process: As the two air streams pass through the heat exchanger, heat is transferred from the warmer air stream to the cooler one. Because the streams move in opposite directions, the temperature difference between them is maintained along the entire length of the exchanger, leading to more efficient heat transfer.
- Temperature Gradient: This configuration ensures that the temperature gradient is highest at the points where the air streams enter and exit the exchanger, enhancing the overall efficiency.
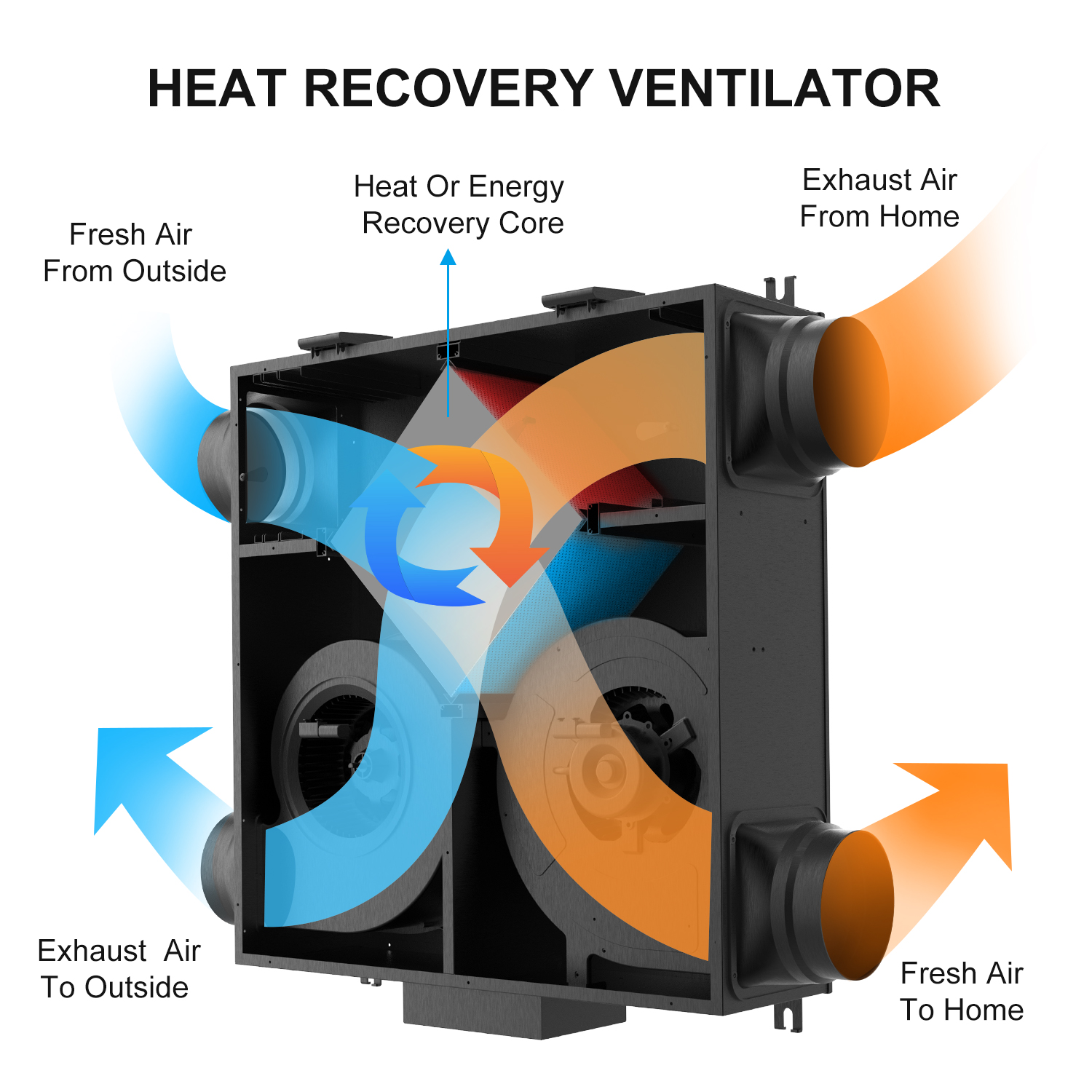
3. Applications:
- Energy Recovery Ventilators (ERVs) and Heat Recovery Ventilators (HRVs): In residential and commercial buildings, these systems use counterflow heat exchangers to recover energy from exhaust air, reducing the need for additional heating or cooling of fresh air intake.
- ERVs: Besides sensible heat, they also exchange latent heat (humidity) between the air streams, which is particularly useful in humid climates.
- HRVs: Focus purely on sensible heat exchange and are ideal for dry climates.
- Industrial Heat Recovery: In industrial processes, counterflow heat exchangers recover waste heat from exhaust gases or air, improving overall energy efficiency and reducing operational costs.
- Example: In a manufacturing plant, exhaust air at high temperatures can preheat incoming fresh air, reducing the energy needed for heating.
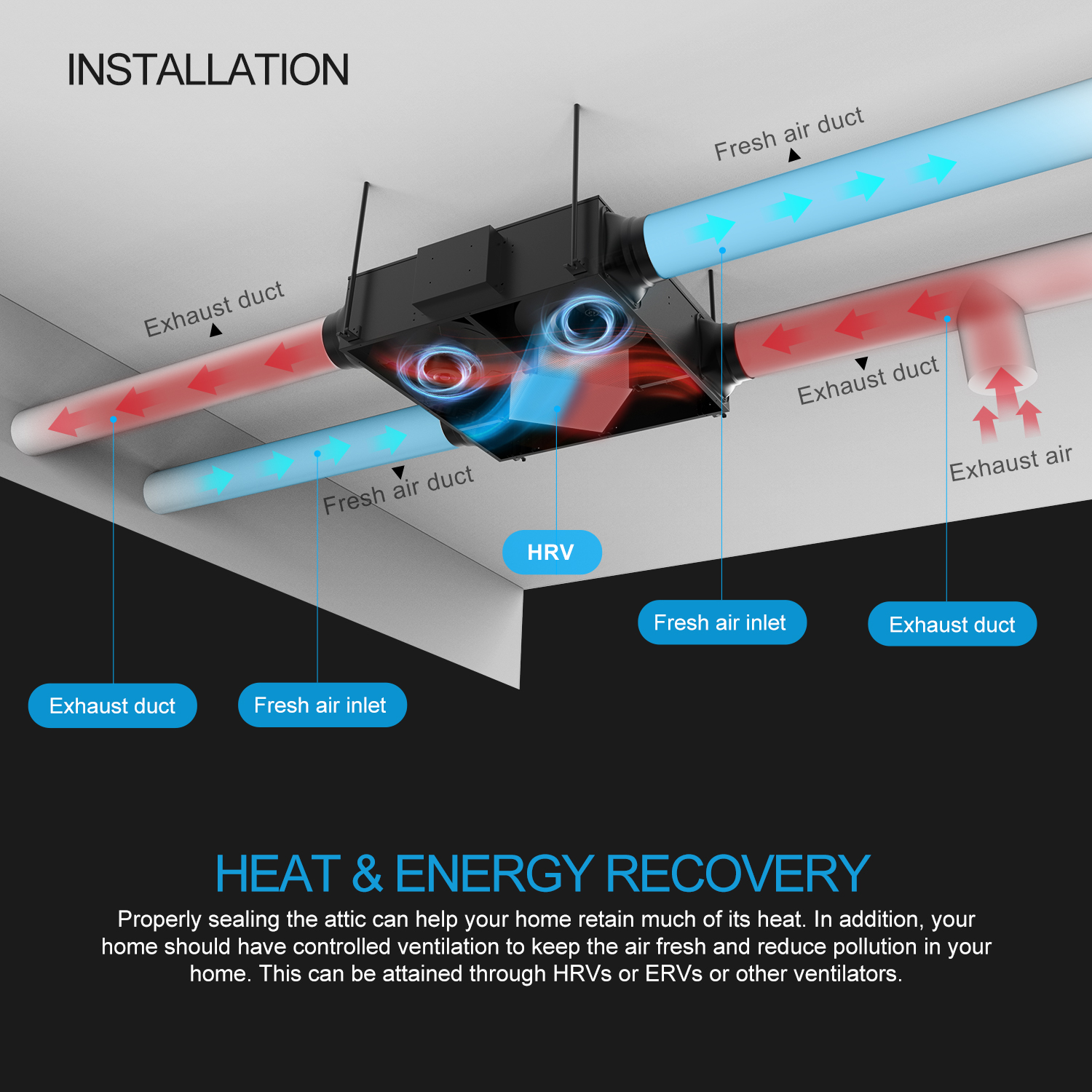
4. Advantages:
- High Efficiency: Counterflow exchangers can achieve thermal efficiencies of up to 90% or higher, depending on the design and operating conditions. This is significantly higher than other configurations like crossflow, which may only achieve efficiencies of 50-70%.
- Compact Design: Because of their efficiency, counterflow heat exchangers can be more compact than other types for the same performance, making them ideal for space-constrained applications.
- Energy Savings: The high efficiency directly translates to reduced energy consumption, which is beneficial for both economic and environmental reasons.
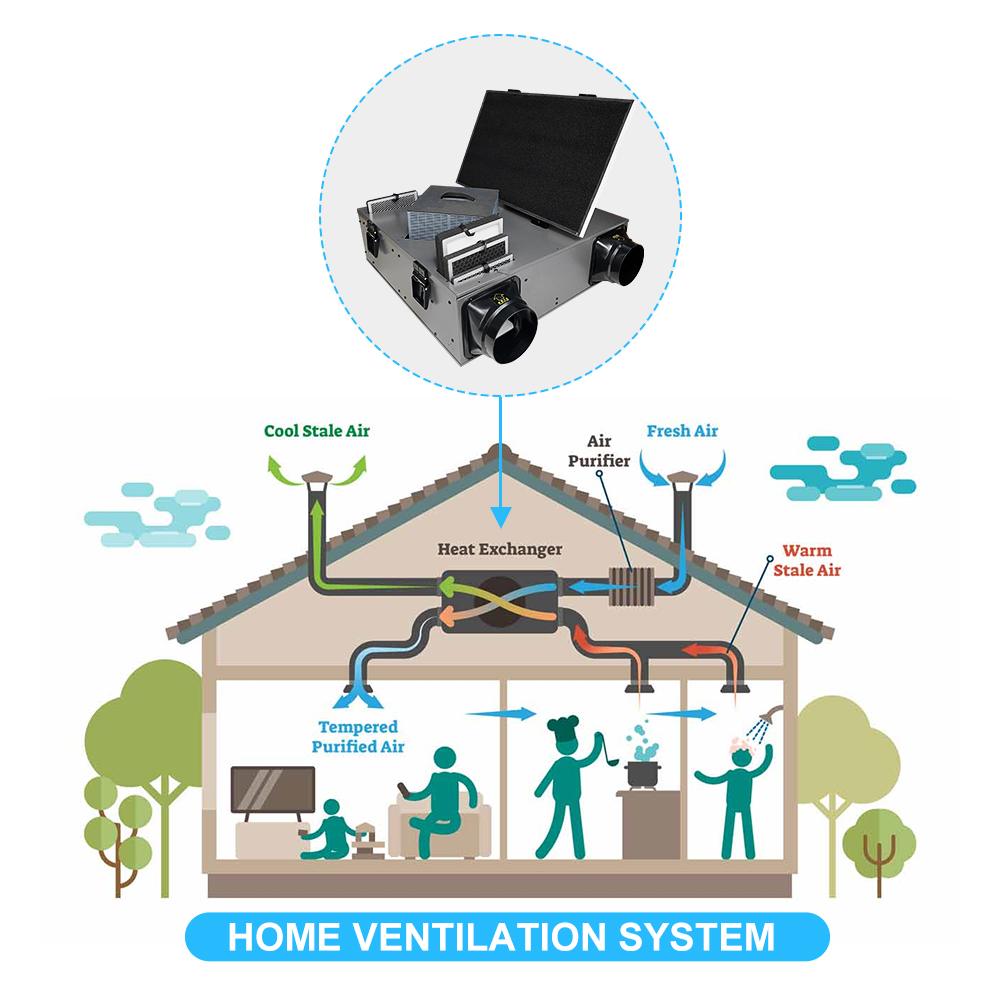
5. Design Considerations:
- Pressure Drop: The design must balance heat transfer efficiency with the pressure drop across the exchanger. A higher pressure drop can increase the energy required to move air through the system, potentially offsetting the energy savings.
- Maintenance and Durability: Materials and construction should be selected based on the operating environment. For example, in corrosive environments, more durable materials or coatings may be necessary.
- Noise: Careful design is needed to minimize noise generated by the air moving through the exchanger, especially in residential or office environments.
6. Emerging Technologies:
- Advanced Materials: New materials with better thermal conductivity and corrosion resistance are being developed to further improve efficiency and durability.
- Integrated Systems: Some modern HVAC systems integrate counterflow heat exchangers with other components, such as heat pumps or desiccant wheels, to optimize overall energy performance.
Counterflow sensible heat exchangers are vital components in modern HVAC systems and industrial applications, offering high efficiency, energy savings, and compact design. By carefully considering the design parameters and application-specific requirements, these exchangers can significantly reduce energy consumption and operating costs.